Custom CNC Machining Factories: Precision Engineering at Its Best
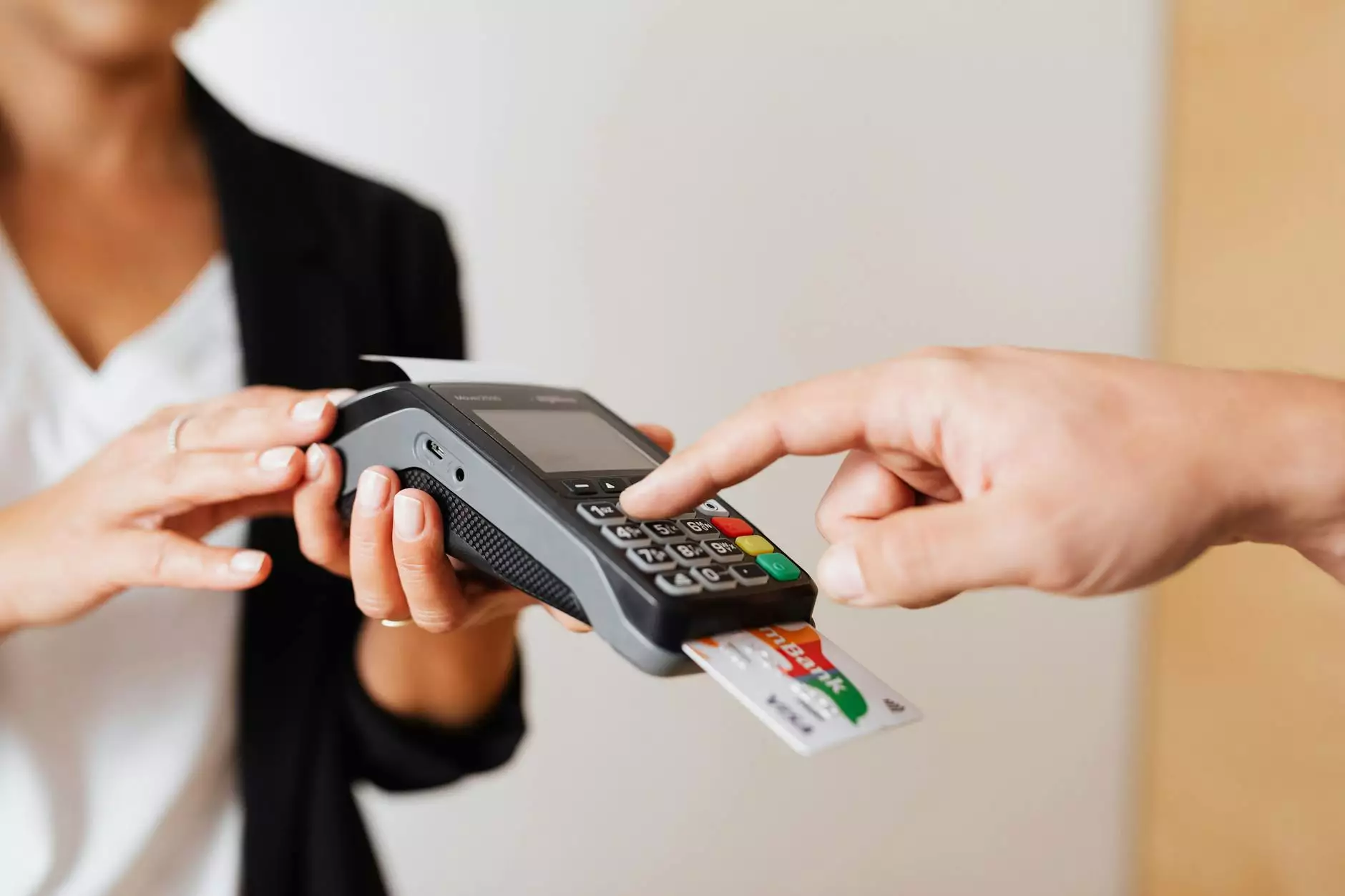
In the world of metal fabrication, the term custom CNC machining factories has become synonymous with precision, quality, and innovation. These specialized facilities utilize advanced computer numerical control (CNC) technology to produce components that meet the strictest standards and specifications. In this comprehensive article, we will explore the ins and outs of custom CNC machining factories, their benefits, applications, and why they are essential for modern manufacturing.
Understanding CNC Machining
CNC machining represents a pivotal advancement in manufacturing technology. Unlike traditional machining processes, CNC machining allows for the automation of machine tools via programmed commands. This process includes the following stages:
- Design: Every project begins with a detailed design, often created in computer-aided design (CAD) software.
- Programming: The design is converted into a machine-readable format, generating precise instructions for the CNC machine.
- Machining: The CNC machine then executes the programmed instructions, cutting and shaping materials with remarkable accuracy.
- Finishing: Post-processing steps, such as polishing and coating, refine the final product.
The Advantages of Custom CNC Machining Factories
Custom CNC machining factories offer a myriad of advantages that elevate them above traditional manufacturing methods. Here are some key benefits:
- Precision: CNC machining is known for its high precision, allowing for tolerances as low as ±0.002 inches. This level of accuracy is essential for industries like aerospace and medical devices.
- Repeatability: Once a CNC program is established, it can be replicated consistently, producing identical parts time after time without the risk of human error.
- Complex Geometries: CNC machining can create intricate designs and complex geometries that would be difficult or impossible to achieve with manual machining methods.
- Material Versatility: Custom CNC machining can work with a variety of materials, including metals, plastics, wood, and composites, making it an ideal choice for diverse applications.
- Speed: The automation of the machining process significantly speeds up production times, allowing factories to meet tight deadlines without compromising on quality.
Applications of Custom CNC Machining
The versatility of custom CNC machining factories makes them pivotal across various industries. Here are some prominent applications:
Aerospace Industry
The aerospace sector requires components that meet stringent safety and performance standards. Custom CNC machining is used to create parts like:
- Engine components
- Structural frames
- Landing gear components
- Interior fittings
Medical Devices
In the medical field, precision is paramount. Custom CNC machining factories produce:
- Surgical instruments
- Implants
- Custom prosthetics
- Diagnostic equipment
Automotive Industry
The automotive industry relies heavily on CNC machining for manufacturing components such as:
- Engine blocks
- Transmission parts
- Suspension components
- Body panels
Quality Control in Custom CNC Machining
Quality control is an integral aspect of custom CNC machining factories. To ensure that every component meets the required specifications, factories implement strict quality control measures. These may include:
- Dimensional Inspection: Utilizing metrology tools such as calipers and CMMs (Coordinate Measuring Machines) to check tolerances.
- Material Testing: Verifying that raw materials meet mechanical and physical requirements.
- Process Monitoring: Continuously monitoring the CNC machines during operation to detect any deviations in the production process.
Investing in Custom CNC Machining Technology
For businesses considering the transition to custom CNC machining, it's vital to recognize that this investment can yield substantial returns. The initial cost for CNC machines and tooling may be significant, but the long-term benefits often justify the expenditure. Key considerations include:
- Cost Efficiency: Reducing operational costs through automation and improved efficiency.
- Scalability: The ability to scale operations up or down based on demand without major reconfiguration.
- Enhanced Capabilities: Gaining access to a broader range of services and techniques through CNC technology.
The Future of Custom CNC Machining Factories
As technology continues to evolve, custom CNC machining factories are poised to see significant advancements. The future may include:
- Smart Manufacturing: Incorporating IoT and AI technology to optimize processes and improve decision-making.
- Sustainability: Greater emphasis on sustainable practices, such as recycling scrap materials and using eco-friendly processes.
- Integrated Solutions: Offering end-to-end solutions that combine design, prototyping, and production all under one roof.
Choosing the Right Custom CNC Machining Factory
When selecting a custom CNC machining factory, it is imperative to consider several key factors:
- Experience: Look for a factory with a proven track record and experience in your specific industry.
- Capability: Ensure that the factory can handle the specific materials and complexities of your projects.
- Customer Service: Choose a factory that prioritizes communication and customer satisfaction, providing updates and support throughout the machining process.
- Certifications: Verify that the factory adheres to international standards such as ISO 9001, ensuring quality management systems are in place.
Conclusion
Custom CNC machining factories have revolutionized the metal fabrication industry with their unmatched precision and efficiency. As businesses strive to improve product quality and reduce lead times, the role of these factories becomes increasingly essential. With a focus on technology, quality control, and customer satisfaction, the landscape of custom CNC machining will continue to evolve, pushing the boundaries of what's possible in manufacturing.
For companies looking to utilize the potential of custom CNC machining, partnering with a reputable factory like DeepMould can be a game-changer. Their dedication to quality and innovation positions them as leaders in the field, helping businesses turn their visions into reality.