Industrial Blade Manufacturing: A Detailed Overview
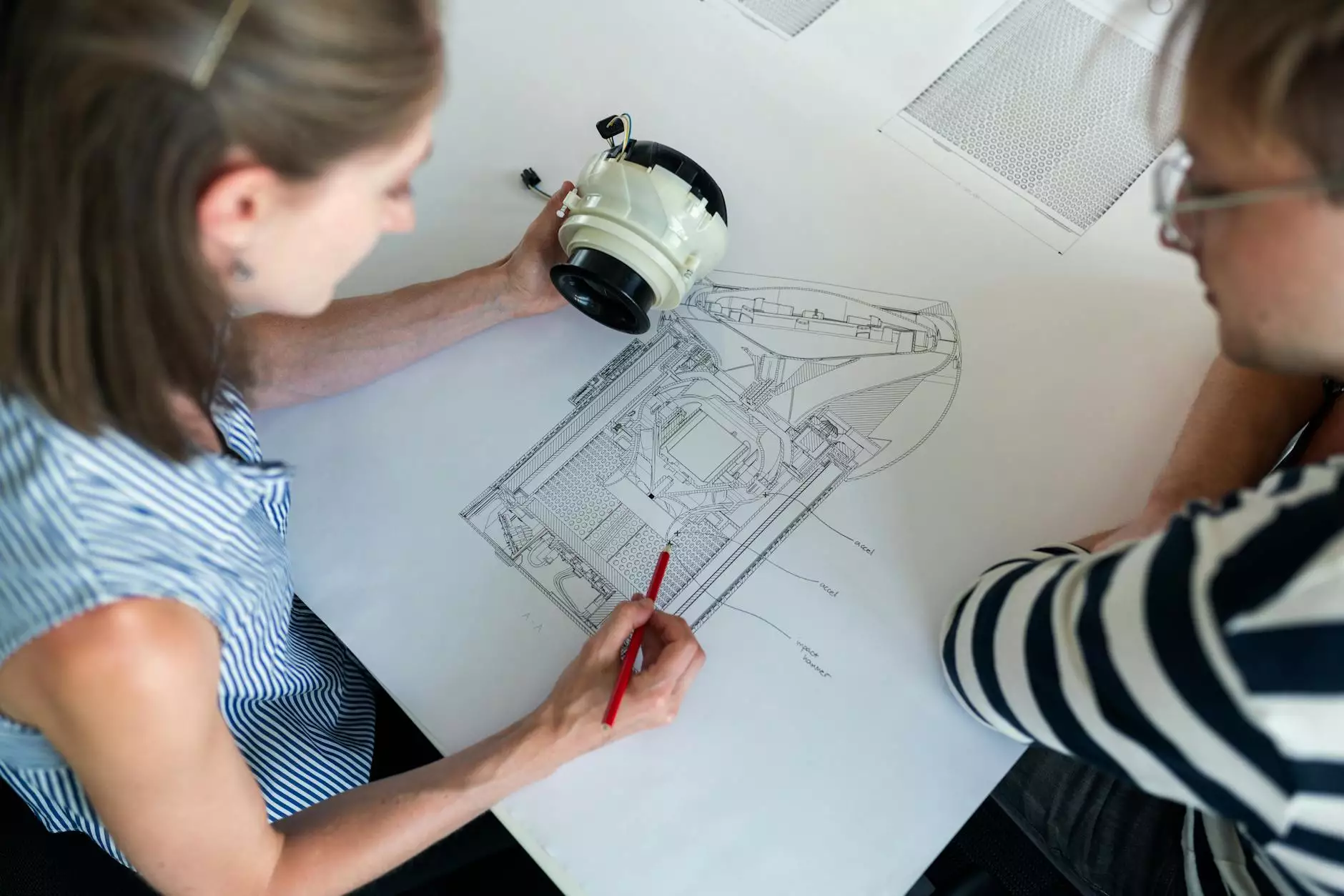
In the realm of modern manufacturing, one cannot underestimate the importance of industrial blade manufacturing. These blades play a critical role across various industries, from food processing to textiles, and their significance continues to grow in a world that demands precision, efficiency, and quality. At szblade.com, we delve into the intricacies of blade manufacturing, exploring everything from materials to techniques while highlighting the professional services of knife sharpening that can enhance your operations.
The Evolution of Industrial Blade Manufacturing
Industrial blades have evolved dramatically over the years. Initially, blades were handcrafted from basic metals, but advances in technology and materials have transformed the industry. Today, industrial blade manufacturing employs sophisticated machinery and high-quality materials that ensure durability and efficiency.
Historical Perspective
- Traditional Craftsmanship: Early blade manufacturing relied heavily on traditional blacksmith techniques.
- Industrial Revolution: The advent of the industrial revolution led to the mechanization of blade production.
- Modern Technologies: Today’s manufacturing processes leverage CNC machines and laser cutting technology for precision.
Key Processes in Industrial Blade Manufacturing
Understanding the processes involved in industrial blade manufacturing is crucial for businesses looking to optimize their production efficiency. Below are the key steps typically involved:
1. Material Selection
The choice of materials is fundamental in determining the performance and longevity of blades. Common materials used in industrial blade manufacturing include:
- High-Speed Steel (HSS): Known for its hardness and resistance to wear.
- Carbide: Offers superior toughness and is ideal for cutting tough materials.
- Stainless Steel: Resistant to corrosion, making it suitable for food processing industries.
- Ceramics: Utilized for their sharpness and wear resistance, particularly in specialized applications.
2. Blade Design and Engineering
During the design phase, engineers use CAD software to create precise specifications for each blade. Factors considered include:
- Blade Geometry: The shape and angle of the blade significantly affect its cutting performance.
- Thickness: Thinner blades are used for precision cutting, while thicker blades provide strength.
- Profile: Tailoring the profile to specific cutting needs enhances efficiency.
3. Manufacturing Techniques
The manufacturing of industrial blades employs various techniques, which can include:
- Stamping: A method where blades are cut from sheet metal using a die.
- Grinding: Processes that refine the blade edge for sharpness and accuracy.
- Heat Treatment: Enhances the hardness and durability of the blade through controlled heating and cooling.
- Coating: Applying protective coatings to reduce wear and corrosion.
Quality Control in Industrial Blade Manufacturing
Quality assurance is pivotal in the industrial blade manufacturing process. Various methods are implemented to ensure that each blade meets stringent industry standards:
- Visual Inspections: Identifying defects and inconsistencies before the blades are finalized.
- Dimensional Testing: Ensuring blades adhere to precise specifications.
- Performance Testing: Conducting tests to verify the durability and effectiveness of blades under operational conditions.
Importance of Knife Sharpening Services
Once blades are manufactured, maintaining their sharpness is essential. At szblade.com, we offer professional knife sharpening services that can significantly enhance the performance of your tools:
The Benefits of Regular Sharpening
- Improved Efficiency: Sharp blades cut more effectively, reducing strain on machinery.
- Cost-Effective: Regular sharpening extends the lifespan of your blades, saving money over time.
- Safety: Dull blades can lead to accidents; keeping them sharp minimizes risks.
Sharpening Techniques
Our expert team utilizes various sharpening techniques to suit different types of blades:
- Honing: A method used to realign the edge of the blade.
- Grinding: Involves removing material to create a sharp edge.
- Scissor Shearing: Special techniques for blade types requiring precise alignment.
Why Choose Professional Services for Industrial Blade Manufacturing and Knife Sharpening?
Choosing professional services, such as those offered by szblade.com, offers numerous advantages:
- Expertise: Our team comprises experienced professionals who understand the nuances of blade manufacturing and maintenance.
- Precision: We utilize state-of-the-art equipment ensuring the highest quality standards in every service.
- Customization: Our manufacturing process is adaptable, allowing us to create bespoke blades tailored to your specific needs.
- Reliability: We stand by our products and services, ensuring you receive support when you need it.
The Future of Industrial Blade Manufacturing
The landscape of industrial blade manufacturing is set to evolve even further with advancements in technology. Innovations such as automated manufacturing, artificial intelligence, and improved materials will revolutionize the industry. Businesses must stay informed about these changes to maintain competitiveness.
The Role of Sustainability
As industries shift toward more sustainable practices, manufacturers are increasingly focusing on eco-friendly methods. This includes the use of recyclable materials and reducing waste in the manufacturing process. Embracing sustainability not only helps the environment but also appeals to conscientious consumers.
Conclusion
In conclusion, the domain of industrial blade manufacturing is not only vast but also pivotal for numerous sectors worldwide. Understanding the processes involved, the importance of quality, and the benefits of professional knife sharpening can significantly impact your business operations. As you seek reliable and proficient services, remember that at szblade.com, we are dedicated to delivering exceptional quality blades and sharpening services that meet the demands of your industry. With a commitment to continuous improvement and innovation, we are poised to navigate the future of blade manufacturing with confidence.